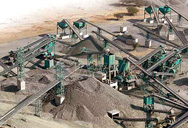
Wet and dry grinding of coal in a laboratory-scale ball mill:
2020.1.1 Abstract. In this study, experimental data for wet- and dry-ground coal samples under wet and dry grinding are characterized by commonly used distribution functions. First, both the R-R and Swrebec functions have superior fitting performances
More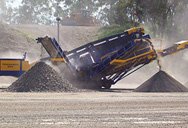
(PDF) MPS mills for coal grinding - ResearchGate
2014.1.1 PDF Two mill systems are employed for most coal grinding applications in the cement industry. These are, on the one hand, vertical roller mills (VRM)... Find, read
More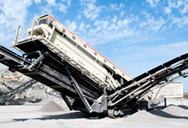
Study on maceral liberation characteristics of ball grinding
The liberation characteristics of long flame coal from the Chinese Shenhua were studied by comparison of ball grinding and rod grinding. First, the effects of grinding time on maceral
More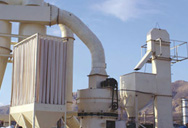
Wet and dry grinding of coal in a laboratory-scale ball mill: Particle ...
2020.1.1 Abstract. In this study, experimental data for wet- and dry-ground coal samples under wet and dry grinding are characterized by commonly used distribution
More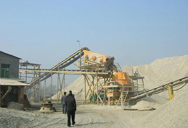
Coal grinding mill, Coal grinding grinding mill - All industrial ...
horizontal grain for coal grinding. Rotational speed: 6,000 rpm. Motor power: 2 kW. Machine weight: 68 kg. ... 200 Lab Mill is used for crushing: Bricks Chemicals Coal Concrete
More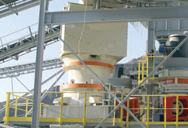
Exploring ball size distribution in coal grinding mills
2014.5.1 Based on the machine learning method, this study analyzed the full process parameters (i.e., ball mill power, fresh ore feed rate, hydrocyclone feed pump power,
More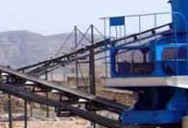
Coal grinding technology: a manual for process engineers.
The wet ball mill grinding system was operated in open circuit, first grinding coal in No. 6 fuel oil and then grinding coal in water. The air swept ball mill grinding system was returned
More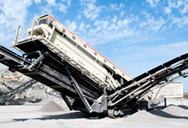
Analysis of coal Mill Dynamic Characteristics Under
1997.8.1 Compared with the raw coal and air flow input, the effect of the mill input airflow temperature on the mill coal grinding process is small, as long as the mill coal
More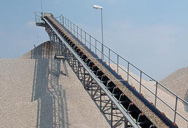
Grinding kinetics of coal in wet ball-milling using the Taguchi method ...
Grinding kinetics of coal in wet ball-milling using the Taguchi method. In this study, the Taguchi method was used to study the influence of feed size, ball diameter, pulp density
More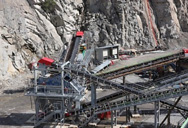
Wet Grinding of Coal in the Szego Mill: Limiting Predictions
Read this article. Results from a systematic grinding study with the SM-320 Szego Mill are reported. A wide range of flow rates, from 750 to 5300 kg/h of coal, at 60–65% solids
More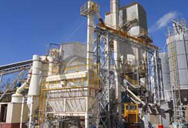
Study on maceral liberation characteristics of ball grinding
The liberation characteristics of long flame coal from the Chinese Shenhua were studied by comparison of ball grinding and rod grinding. First, the effects of grinding time on maceral liberation under the different particle size range, including vitrinite content (VC), vitrinite liberation degree (VLD) and vitrinite monomer content (VMC) were ...
More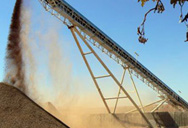
Vertical Grinding Mill (Coal Pulverizer) Explained
A vertical grinding mill consists of the following components: Electric Motor - to rotate the grinding table. The electric motor is often a three phase variable speed drive (VSD) induction motor, but designs vary. Reduction Gearbox
More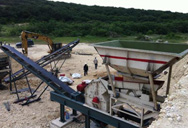
Maximizing wear resistance of balls for grinding of coal
2007.9.10 Grinding periods of 10 h each, up to 70 h total grinding time. At the end of each grinding period, the finer fraction of the coal (under 0.075 μm) was discarded and the charge was completed with new coal. (3) Weighing: At the end of each grinding period, the mill was discharged and the balls were cleaned, dried and weighed to 0.01 g. The ...
More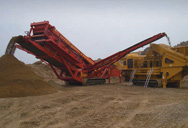
Exploring ball size distribution in coal grinding mills
2014.5.1 The ball size distribution (BSD) in a mill is usually not known, as the measurement of the charge size distribution requires dumping the load and laboriously grading the balls into size classes. Fortunately we had one set of data as discussed below. The general non-availability of BSD necessitates the use of ball wear theory to estimate
More
Modeling of Coal Mill System Used for Fault Simulation
2020.4.7 The variable k gr of the model is the grinding coefficient, which represents the ability of the mill to grind raw coal into coal powder. Under normal operation conditions, the grinding coefficient is related to the grinding roller pressure and grinding current. In the fault simulation process, the grinding coefficient is multiplied by the ...
More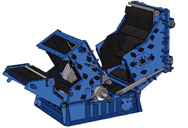
An investigation of performance characteristics and
2020.8.12 Vertical Coal Mill (VCM) is equipment for grinding and pulverizing coal into micron size. Rotary kilns then use the powders as fuel burners. The VCM has a housing section equipped with a lining ...
More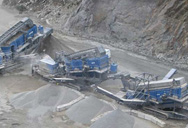
Influence of wood pellets properties on their grinding
2021.6.9 The reduced grinding energy is due to a decreased mill load, which has advantages regarding maintenance costs, mill availability, mill capacity, and milling power costs. A drying step is typically included in biomass-converted suspension-fired power plants, where existing coal roller mills, typically equipped with a classifier system, are ...
More
Modeling of Coal Mill System Used for Fault Simulation
2020.4.7 The variable k gr of the model is the grinding coefficient, which represents the ability of the mill to grind raw coal into coal powder. Under normal operation conditions, the grinding coefficient is related to the grinding roller pressure and grinding current. In the fault simulation process, the grinding coefficient is multiplied by the ...
More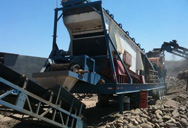
Grinding kinetics of coal in wet ball-milling using the Taguchi method ...
Grinding kinetics of −3.0 + 1.0 mm coal in wet ball-milling were investigated using the breakage rate and primary breakage distribution functions. The deceleration effect for the wet grinding of this coal sample was due to the relatively stronger material (quartz), which had a slower breakage rate compared to the weaker material (organic matter).
More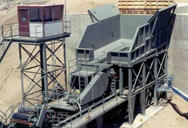
Review on vertical roller mill in cement industry its
2021.1.1 Coal Grinding: Grinding Mill - Vertical Roller Mill or Ball Mill: Coal is ground in Coal mill, which is a fuel for use in Kiln firing: 5: ... As per European cement research academy's project “Future grinding technologies”, out of 1036 orders of grinding mills in 5 years, 58% were for Vertical Roller mill and 40% were for Ball Mill + HPGR ...
More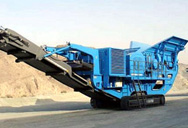
Grindability and combustion behavior of coal and torrefied
2015.9.1 2.3. Grindability test. Grindability was evaluated from the particle size distribution profiles of the coal and each raw and torrefied biomass sample (Bridgeman et al., 2010).A mass of 50 g torrefied sample was ground in a mortar grinder for 15 min.The ground sample was then sieved using a series of four sieves of mesh sizes 75, 150, 425
More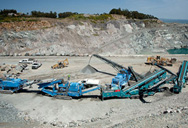
Determination of Selection-for-Breakage Functions in the Batch Grinding ...
A comparison of the results obtained from grinding in a stirred media mill lignite coal samples treated with microwave and untreated samples. Fuel 2011, 90 (2) , ... A simulation model for analysis and design of continuous grinding mills. Powder Technology 1998, 97 (1) ,
More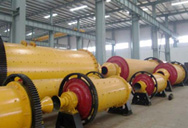
Vertical Coal Mill, Limestone Vertical Mill supplier - Hefei
2023.11.2 90t / h Large Output Coal Grinding Equipment Coal Vertical Mill Working principle of coal vertical mill: The raw coal falls to the center of the grinding disc through the feeding pipe, and the grinding disc rotating at a constant speed disperses and flattens the raw material outwards evenly with the...
More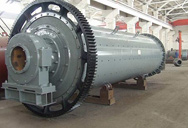
The effects on the grinding parameters of chemical,
2022.1.1 Wet and dry grinding of coal in a laboratory-scale ball mill: Particle-size distributions. Powder Technol. (2020) ... have dealt with methods on vertical mills (Csőke et al., 2003; Shi, 2014; Shi Zuo, 2014; Deniz, 2022). Vertical mills are grinding equipment that has found much more application in a wide range of powder technology in recent ...
More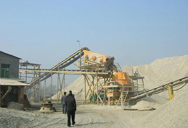
Fine grinding of coal by the turbomilling process. Report of ...
@article{osti_6260270, title = {Fine grinding of coal by the turbomilling process. Report of Investigations/1987}, author = {Davis, E G}, abstractNote = {The Bureau of Mines conducted studies on comminution of bituminous coal to the 2-micrometers particle-size range using the Bureau-developed turbomill. Both plant-grind size (80 pct minus 75 micrometers) and
More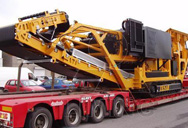
Dry grinding studies of coal in a rod mill - Springer
2018.10.23 Coal by Microbubble Flotation," Virginia Polytechnic Institute and State University, Blacksburg, VA, 17 pp. Dry grinding studies of coal in a rod mill S.Dasand J .S. Murty % Retained 2.0 10.0 21.0 22.0 18.0 6.0 21.0 It Abstract-In this paper, a report is given ofstudies ot!d.ertaken in a laboratory rod mill to obtain the
More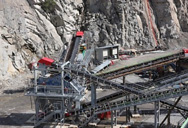
An assessment of grindability index of coal - ResearchGate
2002.4.1 Grindability of coal is a central characteristic of coal which is closely related to pulverizer performance and mill capacity (ACARP, 1998) and is defined as ease of grinding of coal which is, in ...
More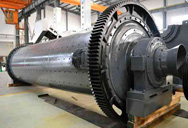
Grinding and combustion characteristics of woody
2014.10.15 A suitable mill type for woody biomass grinding has been sought in laboratory-scale experiments. The selected industrial-scale mill has been modified to increase the capacity. The objective of this experimental study is to establish and demonstrate the woody biomass firing system including mill and burner for pulverised
More