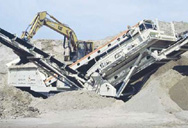
Perfecting the Performance of Secondary Crushers E MJ
2023.2.14 Ideally, the deck on the scalping screen should have a cut point equal to the closed side setting (CSS) of the crusher. The feed size to a secondary crusher is
More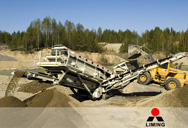
Design of a crushing system that improves the crushing
2016.2.10 Jaw crushers are sized on the basis of the maximum particle size to be crushed and/or the tonnage rate to be crushed. Maximum particle size should not exceed
More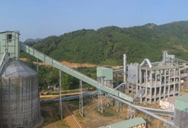
TECHNICAL NOTES 5 CRUSHERS - 911 Metallurgist
2017.4.18 Figure 5.1 Schematic diagram of a crusher showingg the open- and closed-side settings. 5.1 Jaw and Gyratory Crushers. Jaw and gyratory crushers are
More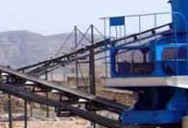
1 Crushing - Springer
2017.8.25 The size to which particles are reduced is governed by three criteria: (i) the required product size if simple sizing only is desired; ... and secondary or intermediate
More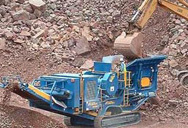
Simulation of particle flows and breakage in crushers using DEM
2015.4.1 The DEM method, including a particle replacement breakage model, has been successfully demonstrated using a broad range of existing compression based
More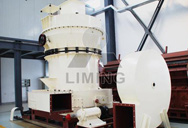
Evaluation of size reduction process for rock aggregates in cone crusher
2020.6.4 The size reduction process of rocks in cone crushers is one of the most important issues, particularly for the secondary and tertiary stages of crushing
More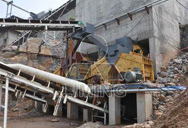
Secondary Crushing Equipment - 911 Metallurgist
2016.2.28 The term “secondary crushing” has become well established and familiar through long usage; it applies to the crushing stage, either single or multiple, which
More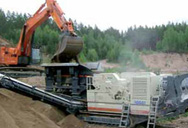
Secondary Impact Crushers – MEKA
Crushing Screening Plants. Crushers. Secondary Impact Crusher. MEKA MSI Series Secondary Impact Crusher is ideally suited to crush soft to medium hard materials down to a highly cubical, well graded product
More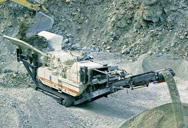
Simulating a laboratory-scale cone crusher in DEM using
2020.7.15 The proportion of each material at the discharge of the crusher for different blends was equivalent to the proportion being fed to the crusher, indicating that the soft
More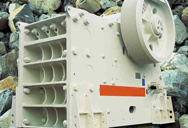
Evaluation of size reduction process for rock aggregates in cone crusher
2020.6.4 The size reduction process of rocks in cone crushers is one of the most important issues, particularly for the secondary and tertiary stages of crushing operations. In this study, 17 different rock types were considered for the evaluation of their size reduction variations that occurred in a laboratory-scale cone crusher. Based on several
More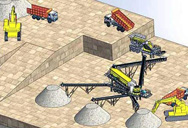
Experimental Investigation of Particle Size
2022.9.29 This study examines the particle size and distribution of the main chemical components of gangue during the crushing process. Coal mine gangue was chosen as the research object, and its particle size
More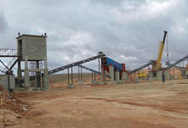
Size Reduction-1: Grinding – Unit Operations in
The size reduction of large pieces of solid materials into small lumps is done by crusher which is commonly used for heavy work. A primary crusher may break large pieces of solid materials into 6 to 10 inch lumps. A secondary
More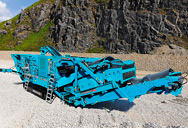
Primary Crusher vs. Secondary Crusher: Understanding Their
2023.2.28 The primary crusher is responsible for breaking down larger rocks and stones into manageable sizes, while the secondary crusher further refines these particles into the desired product. While both types of crushers are used in a variety of real-world applications, understanding their differences and when to use each type is crucial for ...
More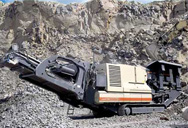
Crushing Products Size and Shape -What to Expect - 911
2016.2.26 The difference between the cumulative percentages at the 3.5″ and 1.5″ points on the curve gives us the amount, of such product to be expected from the output of the primary crusher This is 85 minus 43, or 42% of the primary crusher product. If our problem had covered a crushing condition calling for 80 instead of 85% passing the
More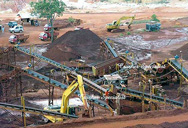
Evaluation of blast fragmentation effects on jaw crusher
2021.9.21 After the statistical analysis of collected data pairs, the relationship between the throughput of the jaw crusher and particle size distribution properties of blasting was determined. Considering the relationships, it is noted that, P 50, P 80, and P top sizes of the blasted rock have a significant relationship with the jaw crusher performance.
More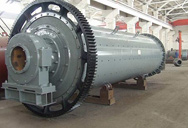
Secondary Crushing - WOMP
2021.4.23 Secondary applications are dependent on the primary crusher to provide a targeted feed size, so fl uctuations in the run-of-mine (ROM) ore can contribute considerably. Changes in gradation (i.e., feed getting coarser or finer), hardness, moisture or, if the work index increases or decreases, can trigger adjustments in screen panels as well as ...
More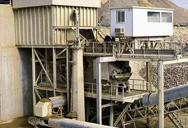
AMIT 135: Lesson 5 Crushing – Mining Mill Operator Training
The purpose of the primary crusher is to reduce the ROM ore to a size amenable for feeding the secondary crusher or the SAG mill grinding circuit. The ratio of reduction through a primary crusher can be up to about 8:1. Feed: ROM up to 1.5 m. Product: -300mm (for transport) to -200mm (for SAG mill) Feed Rate:
More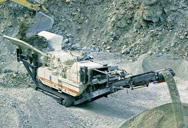
Perfecting the Performance of Secondary Crushers E MJ
2023.2.14 Ideally, the deck on the scalping screen should have a cut point equal to the closed side setting (CSS) of the crusher. The feed size to a secondary crusher is typically in the range of 50 mm to 250 mm (up to 300 mm). If the capacity is higher, the acceptable feed size gets larger. After crushing, the product is in the range of 0-60 mm
More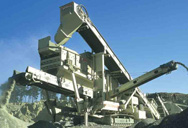
Complete Lecture about Crushers in Cement Industry
Coarse size reduction:6000 kg of quartzite was crushed in a cone crusher for one hour; a feed particle size of 5-50 mm was reduced to a pr,oduct particle size of 0- 5 mm. The crusher’s power input was 18 kWh, i.e. a specific energy consumption of ... The width of the crusher’s discharge opening e (Fig. 3.3.a) is being measured from the top ...
More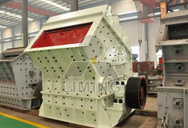
Comminution - University of Technology, Iraq
2018.1.19 The most common type of secondary crusher is the cone crusher. Crusher can be classified to; ... The feed is at one end of the cylinder and the discharge is at the other. Industrial ball mills can be as large as 8.5 m (28 ft) in diameter. ... To prepare product that meets particle size specifications required for the market
More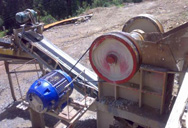
AMIT 135: Lesson 6 Grinding Circuit – Mining Mill
AG/SAG mills are normally used to grind run-off-mine ore or primary crusher product. Wet grinding in an AG/SAG mill is accomplished in a slurry of 50 to 80 percent solids. 2D and 3D simulations of particles in a SAG Mill
More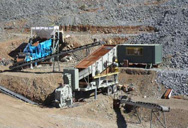
Jaw Crusher Explained - saVRee
Size Reduction) A crusher is a machine designed to reduce the size of large rocks to smaller rocks, gravel, sand, or rock dust; this is essential for efficient transport of the product via conveyors etc. Crushing is the first of
More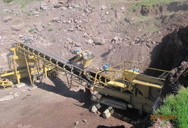
Minerals Free Full-Text Pre-Processing to Increase the
2022.6.6 A total of 120 t of Cristalino ore was prepared and sent to CIMM, where it was crushed and screened prior to grinding tests. The processing equipment included a 1.83 m (8′) diameter by 0.61 m (2′) length AG/SAG mill equipped with a 20 kW motor, a cone crusher, a 0.91 m (3′) diameter by 1.22 m (4′) length ball mill equipped with a 15 kW ...
More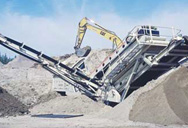
Gyratory and Cone Crusher - ScienceDirect
2016.1.1 All other variables being the same, establish a relation between productivity and the set at the discharge opening. 5.8. A secondary crusher (size 16–50) with approximate feed opening of 41 cm × 40 cm had an eccentric throw of 1.9 cm. Gyrating at 225 rpm it crushed limestone with an open setting of 3.8 cm. Calculate the percent
More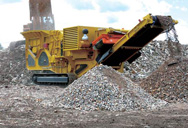
Stone crusher plant Henan Deya Machinery Co., Ltd.
2022.7.5 2.1 Primary crushing stage. 2.1.1. Currently, there are three main types of primary stone crushers: jaw crushers, impact crushers and gyratory crushers. The impact crusher, as a primary crusher, is only suitable for medium to soft rocks, such as limestone, and thus its use is limited. Large jaw crushers with a maximum feed length of up to 1m ...
More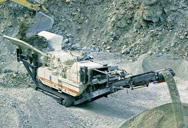
m/sbm crusher discharge particle size adjustment.md at
Contribute to legaojm/m development by creating an account on GitHub.
More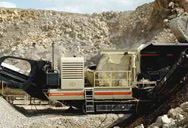
Everything you need to know about Crushers in Cement
The roller crushers are used for moist and sticky materials. Generally the machines have to be rigid enough to crush also hard inclusions. As the reduction ratio is only about 5:1 a 2-stage crushing is required in most applications. Fast running type crushers like hammer and impact crushers are the simplest and cheapest solution, whenever the ...
More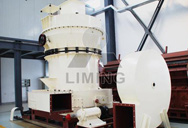
Crusher - an overview ScienceDirect Topics
The secondary crusher is mainly used to reclaim the primary crusher product. The crushed material, which is around 15 cm in diameter obtained from the ore storage, is disposed as the final crusher product. The size is usually between 0.5 and 2 cm in diameter so that it is suitable for grinding. Secondary crushers are comparatively lighter in ...
More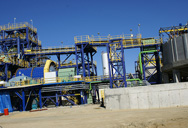
7 Types of Stone Crusher and How to Choose the Best?
2021.9.23 Advantages: large crushing ratio, high efficiency, low energy consumption, less dust, uniform product size, stable operation, low failure rate, and not easy to be crushed. Disadvantages: The structure and maintenance are more complicated, the body is high, and the price is expensive. 3. Impact Crusher.
More