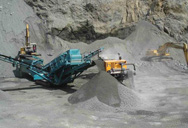
Comminution and classification technologies of iron ore
2022.1.1 Abstract. Hematite and magnetite, the two predominant iron ores, require different processing routes. High-grade hematite direct shipping ores generally only require crushing and screening to meet the size requirements of lump (typically between 6 and
More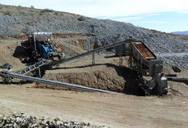
The six main steps of iron ore processing - Multotec
1. Screening We recommend that you begin by screening the iron ore to separate fine particles below the crusher’s CSS before the crushing stage. A static screen is used to
More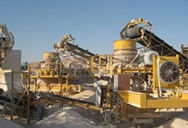
(PDF) ORE SEPARATION BY SCREENING
2017.3.3 Screening is done by dry screening and wet sc reening methods. ... Sieving is a process of separation of the ore material into
More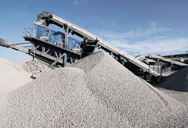
Developments in iron ore comminution and classification
2015.1.1 As shown in Figure 8.7, the proposed processing plant will include the following components: three remote primary/secondary crushing stations, overland
More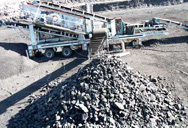
PROCESS MINERALOGY STUDIES OF LOW GRADE IRON
2023.2.18 This article presents the process mineralogy studies of three low grade iron ore samples, with distinct alteration degree and complex mineralogy, targeted for the
More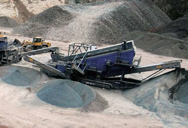
Simec Mining 950tph Iron Ore Beneficiation Wash
950tph iron ore beneficiation wet processing project in South Australia. Learn more about this award-winning CDE and Simec Mining project.
More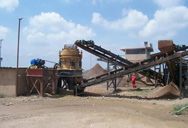
Developments in nonmagnetic physical separation technologies for ...
2015.1.1 The processing of iron ore requires physical processes that help ensure conformation to sizing specifications and where required help the ore achieve grade
More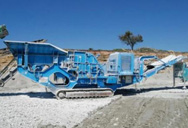
Influence of Grinding and Classification Circuit on the Performance
2019.12.17 ABSTRACT. Process flowsheet has a greater effect on equipment performance and operating conditions. For this purpose, performance of two iron ore
More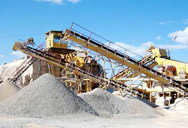
Metso Outotec to provide 'unique' sustainable screening tech to iron ...
2021.9.17 Metso Outotec says it will supply unique sustainable screening technology for an iron ore project in the Southern Hemisphere. ... The innovative and patented BSE
More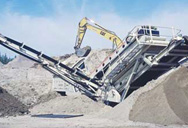
Characterisation and Processing of Some Iron Ores of
2017.8.25 iron oxide ores necessitated the processing and utilization of sub and low grade iron ore lumps and fines and mine waste dumps. The previous works by IBM [1,
More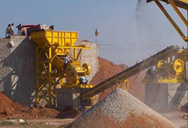
The six main steps of iron ore processing - Multotec
Six steps to process iron ore. 1. Screening. We recommend that you begin by screening the iron ore to separate fine particles below the crusher’s CSS before the crushing stage. A static screen is used to divert the fine particles for crushing. This step prevents overloading the crusher and increases its efficiency.
More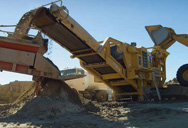
Iron Ore Processing
2017.11.17 Table 2: Results of scrubbing , washing and wet screening of sample crushed t o -5 mm Jigging of -5+1 mm fraction Jigging of -5+1mm fraction was carried out and the result is portrayed in Fig 2. Jigging was done at a ... Iron Ore Processing 503. 5 Tabling of -1+0.1mm fraction The (-1+0.1 mm) fraction so obtained from scrubbing and
More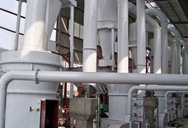
Iron Ore Geoscience Australia
2019.11.4 Iron (Fe) is a metallic element that constitutes 5.6% by weight of the Earth's crust and is the fourth most abundant element in the crust. Iron ores are rocks from which metallic iron can be economically extracted. The principal iron ores contain hematite (Fe 2 O 3) and magnetite (Fe 3 O 4 ). Hematite is an iron oxide mineral.
More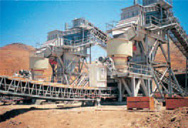
Dry and Wet Screening in Mining: What are the Differences?
2018.2.14 Two deck models augment the process while keeping the cost of the equipment range manageable. Meanwhile, the wet “slurry” produced by the sprinkler nozzles necessitates a dewatering stage. Having said that, there comes a point when dry screening is no longer viable. For example, powdered coal requires a wet screening stage.
More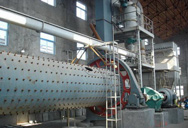
What is dry screening iron ore? - LinkedIn
Published Mar 30, 2023. + Follow. Dry screening of iron ore refers to the process of removing impurities and unwanted materials from the ore through the use of various screening techniques. This ...
More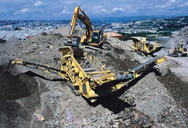
(PDF) Beneficiation and flowsheet development of a low grade iron ore ...
2020.12.1 In the present study a detailed characterization followed by beneficiation of low grade iron ore was studied. The Run of Mine (R.O.M) sample assayed 21.91 % Fe, which is very low grade in nature.
More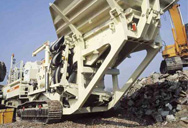
Beneficiation of Iron Ores – IspatGuru
2014.4.3 Fig 3 Types of processing ores. The wet processing (Fig 4) is normally practiced for low / medium grade (60 % Fe to 63 % Fe) hematite iron ore. The wet process consists of multi-stage crushing followed by different stages of washing in the form of scrubbing and / or screening, and classification etc., but the advantage is only partial
More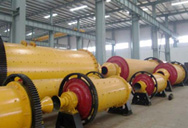
(PDF) ORE SEPARATION BY SCREENING - ResearchGate
2017.3.3 Screening is done by dry screening and wet sc reening methods. ... Sieving is a process of separation of the ore material into multiple grades by particle size [1]. The screen is a vibrating ...
More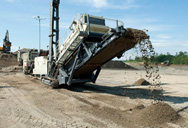
Dry deep screening of spodumene and its mineral processing
2022.3.30 Yu et al. conducted a 3-mm screening test for iron ore using a circular vibrating flip-flow screen (Yu et al., 2020). Akbari proposed dry separation equipment named SIU Airable and conducted screening tests of 1 mm and 2 mm, with good results (Akbari et al., 2020). ... A combined process of dry–wet two-stage desliming, gravity separation, and ...
More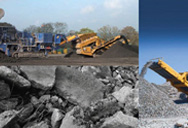
Influence of Grinding and Classification Circuit on the Performance
2019.12.17 ABSTRACT. Process flowsheet has a greater effect on equipment performance and operating conditions. For this purpose, performance of two iron ore beneficiation plants with the same equipment and feed characteristics but different arrangements in the grinding and classification circuit has been investigated.
More
Developments in nonmagnetic physical separation technologies for ...
2015.1.1 The processing of iron ore requires physical processes that help ensure conformation to sizing specifications and where required help the ore achieve grade targets. The sizing separation of iron ore is achieved through the comminution and screening processes described in Chapter 8. This chapter is concerned with the further physical
More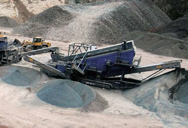
(PDF) Case Study of Dry HPGR Grinding and
2019.2.5 The first difference between the two plants was the screening type of HPGR product. Wet screening in the second plant caused higher classification efficiency, decreasing the circulating load ...
More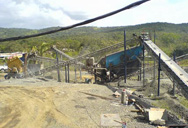
Selection rules for screening operations of mineral processing ...
2021.2.25 (4) Dewatering screening uses the broken and bulky materials (such as clear slurry, mud, ore pulp, etc.) accompanied by large amounts of water as the screening raw materials, and the screening for removing the liquid phase is called dehydration screening. For example: wet ore beneficiation or coal beneficiation needs to be carried
More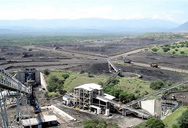
Mineral Processing ScienceDirect
Hence, to meet the growing steel demand, the demand for iron ore is also increasing. ... a general practice adopted by the majority of steel companies has been the utilization of medium- to high-grade ore for iron-making process. This was mainly achieved by selective mining of high-grade ore, keeping the cut-off to approximately 55% Fe. However ...
More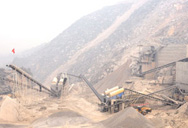
RTZ Iron Ore Mine, Hamersley Basin, Western Australia
2000.4.3 The Hamersley Basin mining area lies in the Pilbara region of north-west Western Australia, 1,100km north of Perth. Through its wholly owned subsidiary, Hamersley Iron Pty, Rio Tinto operates five major producing mines in this area: Mount Tom Price, Marandoo, Brockman, Paraburdoo and Yandicoogina, while the company is in a 60/40%
More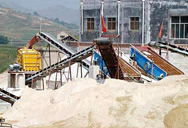
Iron Ore Processing, General SpringerLink
2022.10.20 The iron ore processing industry produces usable concentrations of iron-bearing material by removing nonferrous rock (gangue) from low-grade ore. In the United States, predominant iron ore is taconite which is a hard, banded, low-grade ore. Ninety-nine percent of the crude iron ore produced in the United States is taconite.
More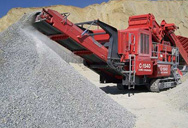
(PDF) Reverse flotation studies on an Indian low grade iron ore
2010.4.1 The Tilden mine operation, Cleveland Cliffs Company employed cationic flotation as part of their iron ore beneficiation process [7]. Many researchers [61][62] [63] have proposed that silica and ...
More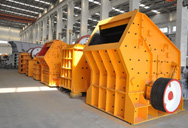
Oremax - Iron Ore washing and Limestone beneficiation...
2023.10.31 By introducing our customised process improvement package we will facilitate the processing of lower grade ores. By reducing your cut-off grade, we will deliver significant efficiencies to your ore processing operation. Maximise the recovery of minerals. Minimise wastage of water. Maximise the value of your minerals. Oremax BROCHURE.
More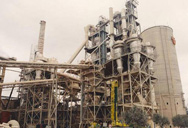
McLanahan Ore Washing and Machine Selection
2021.7.15 Rotary Scrubbers may range in diameter from 8' (2.5m) to 18' (5.0m) and lengths from 8' (2.5m) to 60' (18m) with aspect ratios (L/D) ranging from 1.8 to 3.0. Scrubbers can be sized to process up to 5,000 tph of ore. Improved washing can be accomplished by. Adjusting the water rate to the Scrubber.
More