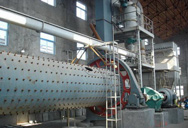
Ball Mill - an overview ScienceDirect Topics
The ball mill contains a hollow cylindrical shell that rotates about its axis. This cylinder is filled with balls that are made of stainless steel or rubber to the material contained in it. Ball mills are classified as attritor, horizontal, planetary, high energy, or shaker.
More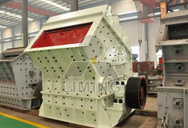
Calculate and Select Ball Mill Ball Size for Optimum Grinding
2013.8.2 Calculate and Select Ball Mill Ball Size for Optimum Grinding. In Grinding, selecting (calculate) the correct or optimum ball
More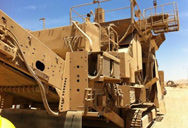
Grinding in Ball Mills: Modeling and Process Control
2012.6.1 PDF The paper presents an overview of the current methodology and practice in modeling and control of the grinding
More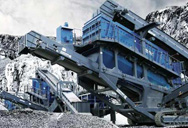
Ball mill - Wikipedia
Description Benchtop ball mill Laboratory scale ball mill High-energy ball milling A ball mill, a type of grinder, is a cylindrical device used in grinding (or mixing) materials like
More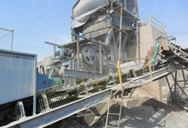
(PDF) Grinding Media in Ball Mills-A Review
2023.4.23 One of the most used tumbling mills is the ball mill. This paper reviews different types of grinding media that have been developed and improved over the years and their properties. Also...
More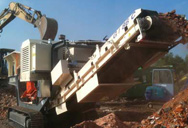
Practical modern techniques for the design of
A number of modern techniques suitable for the design of crushing and grinding circuits are described. The methods are based on extensive use of mathematical models of
More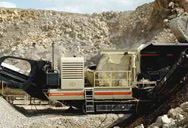
An analysis of the selection function for mills using balls as
1991.10.1 An analysis of the selection function for mills using balls as grinding media - ScienceDirect Article preview Abstract References (24) Cited by (25) Powder
More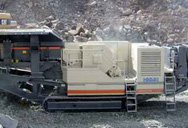
Ball Mill - an overview ScienceDirect Topics
The ball mill is a tumbling mill that uses steel balls as the grinding media. The length of the cylindrical shell is usually 1–1.5 times the shell diameter (Figure 8.11 ). The feed can be
More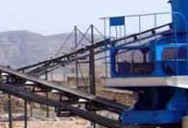
Closed and Open Circuits Ball Mill for Cement,
We bring forth a highly advanced Ball Mill, specifically engineered for both wet as well as dry cement grinding applications. Classified depending on the circuit design, bearing, grinding type and drive, the selection is made on
More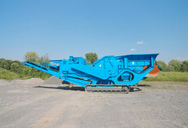
Ball milling as a synthesis method - Aalto University Wiki
2022.4.4 Ball mills can be classified into high-energy ball mills and low-energy ball mills by their rotation speed. Selection of certain ball mill depends on used technique; MA, MM or MD. However, some ball mills can be utilized for all three of these techniques. Table 2 presents the most common ball mills and their energy types. [1, p.26] [4] Table 2.
More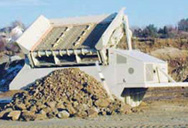
Comminution Theory Process Equipment - 911
2016.10.20 Rod mills should have a length greater than the diameter to avoid entanglement of rods. The construction of ball mills is different in that the diameter may be larger, equal to, or smaller than the length. The
More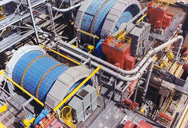
Ball Mill - an overview ScienceDirect Topics
Generally, filling the mill by balls must not exceed 30%–35% of its volume. The productivity of ball mills depends on the drum diameter and the relation of ∫ drum diameter and length. The optimum ratio between length L and diameter D, L:
More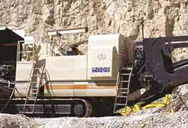
Selection of Rod Mills, Ball Mills, and Regrind Mills
Selection and Sizing of Autogenous and Semi-Autogenous Mills Barratt, D. / Sherman, M. / Society for Mining, Metallurgy, and Exploration et al. 2002 print version
More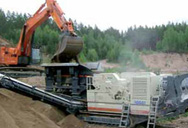
Practical modern techniques for the design of comminution
Rowland C.A. Selection of rod mills, ball mills, pebble mills and regrind mills. In: Design and Institution of Comminution Circuits. A.L. Mular and G.V. Jergensen (Editors). New York AIME, 1982, p. 393–438. Google Scholar Flavell M.D. Scientific methods to design crushing and screening circuits. Mining ...
More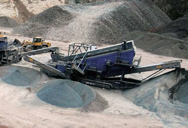
How to choose the ball loading and loading ratio of ball mill?
Tilting current is needed for ball mill production, so it is more appropriate to load balls between one third and one half, and the most ideal is close to one half. According to the actual results of laboratory, when the filling quantity of steel balls in cylinder is 40%, the output is the highest, while the filling rate of steel balls in ...
More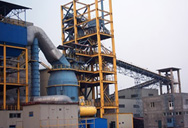
CALCULATION OF THE REQUIRED SEMIAUTOGENOUS MILL
ball mill circuit (WAM — CDBM) In the framework of the discussed method, total SEC in WAM — CDBM circuit is found based on total SEC in a con-ventional circuit including medium and fine crushing, and rod and ball milling. Upon comminution of the initial plant’s feed (coarse crushing discharge) up to ball milling I discharge, the
More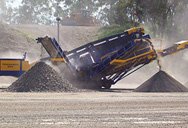
Energies Free Full-Text Energy-Efficient Advanced Ultrafine
2023.7.10 The present literature review explores the energy-efficient ultrafine grinding of particles using stirred mills. The review provides an overview of the different techniques for size reduction and the impact of energy requirements on the choice of stirred mills. It also discusses the factors, including the design, operating parameters, and feed material
More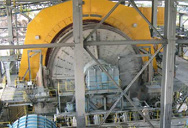
EFFECT OF BALL SIZE DISTRIBUTION ON MILLING PARAMETERS
various mill load conditions (D=195 mm, d=25.4 mm, c=0.7) 41 3.1 Snapshot of the laboratory mill 44 4.1 Selection functions as obtained for three media diameters grinding mono-sized coal materials. In this case (-2360 +1700 microns) 54 4.2 Effect of ball diameter on the selection function 55 4.3 Reduced selection function graph 56
More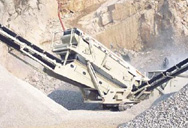
Minerals Free Full-Text Study on the Selection of
2016.4.26 It is evident that the initial selection of a ball mill size of Φ5.03 m × 8.84 m produced 61.62% −0.074 mm materials, but the cycling charge was only 240.9%, indicating this size was too big. A slight
More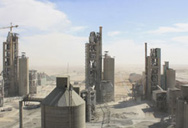
The Effect of Ball Size Diameter on Milling Performance
size ball mill was used with ball media of sizes 10 mm, 20 mm and 30 mm respectively. Quartz was the material used to perform the experiment and was arranged into 3 mono-sizes namely -8 mm +5.6 mm, -4 mm +2.8 mm and-2 mm +1.4 mm for the experiment. A mill run having a mixture of the 3 ball diameter sizes was also conducted. It was
More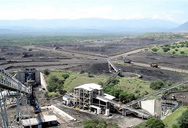
Impact of ball size distribution, compartment configuration, and ...
2022.11.1 In the context of full-scale continuous cement ball milling, there is no exact rule for ball selection; rather, the cement industry designs the mixture of ball sizes and BSD on the basis of their experience along with recommendations from the mill machine suppliers (e.g., FLSmidth, 2012, FLSmidth, 2014) and (empirical) Bond’s approach
More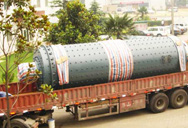
Grinding in Ball Mills: Modeling and Process Control - Sciendo
Keywords: Ball mills, grinding circuit, process control. I. Introduction Grinding in ball mills is an important technological process applied to reduce the size of particles which may have different nature and a wide diversity of physical, mechanical and chemical characteristics. Typical examples are the various ores, minerals, limestone, etc.
More
A Review of Alternative Procedures to the Bond Ball Mill ... - MDPI
2021.7.12 Determining the Bond index using the Fred Bond method [1,2] is considered the state-of-the-art methodology for mill calculations and a critical process parameter in raw materials selection and grinding process control.Although it is usually referred to as a standard test, no ISO (International Organization for Standardization) or
More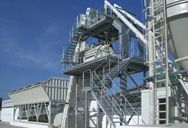
Selection of Rod Mills, Ball Mills and Regrinding Mills PDF
134-MINING ENGINEERING, FEBRUARY 1955. Selection of Rod Mills, Ball Mills and Regrinding Mills - Free download as PDF File (.pdf), Text File (.txt) or read online for free. Selection of Rod Mills, Ball Mills and Regrinding Mills.
More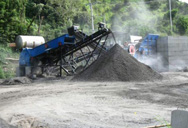
Mill drive selection for semiautogenous grinding mills
ball mills, 18x27 drive with an air clutch. motor, $602,000 6050 D Primary SAG, 34x1 6 Two vafiable speed dc motors coupled mill, $4 million 22,500 to a gear drive with air clutches. motor, $1.28 million each 6000 Two secondary ac synchronized motors coupled to a gear mill, $2.5 million ball mills, 18x27 drive with an air clutch, motor ...
More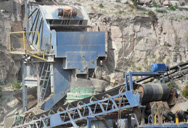
Grinding Machines: Types and Selection Principles - Mining-pedia
2020.9.22 The processing capacity of ball mills and rod mills is usually calculated by volumetric method or power consumption method, and the selection of ore mill should meet the following requirements: 1) Rod mills are mostly used for rough grinding, with a discharge particle size of 1~3mm, which can be ground to 0.5mm in a gravity separation
More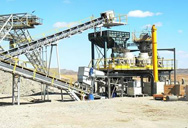
Grinding Media in Ball Mills-A Review - Preprints
2023.4.24 continuous ball mills. In an experiment conducted using a wet laboratory continuous ball mill filled with pebbles, cyl-inders and balls of equivalent volume and a 95% calcite feed combined with a 5% quartz, ball load, density and shape were varied. It was shown that decreasing the ball load by 0.5 by weight also decreased the residence time
More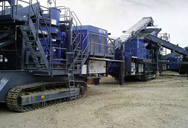
Key considerations when selecting a mill lining system Weir
Ball mills, conversely, contain grinding media up to 50mm in diameter, occupying between 25% - 40% of mill chamber volume. To effectively reduce material size, each type of mill needs to generate different charge load actions, or
More