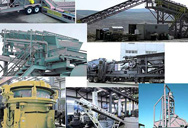
Ball Mill - an overview ScienceDirect Topics
The ball mill contains a hollow cylindrical shell that rotates about its axis. This cylinder is filled with balls that are made of stainless steel or rubber to the material contained in it.
More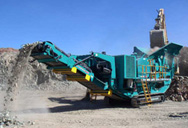
Online Course: Ball Mill - Basic Learner’s Course - FLSmidth
The course contains: 1. Chapters on safety around a ball mill 2. An overview of a ball mill 3. A ball mill’s components and the components’ functions, and on 4. Cement grinding systems with primary focus on closed circuit operation. This clip is on rotation,
More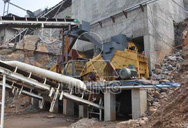
Ball mill - Wikipedia
A ball mill, a type of grinder, is a cylindrical device used in grinding (or mixing) materials like ores, chemicals, ceramic raw materials and paints. Ball mills rotate around a horizontal axis, partially filled with the material to be ground plus the grinding medium. Different materials are used as media, including ceramic balls, flint pebbles, and stainless steel balls. An internal cascading effect reduces the
More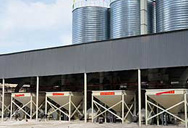
Ball Mills - 911 Metallurgist
2017.2.13 CERAMIC LINED BALL MILL. Ball Mills can be supplied with either ceramic or rubber linings for wet or dry grinding, for continuous or batch type operation, in sizes from 15″ x 21″ to 8′ x 12′. High density ceramic linings of uniform hardness male possible thinner linings and greater and more effective grinding volume.
More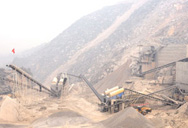
Ball Mill Principle, Construction, Uses, Advantage, Disadvantage
2021.8.17 C. Ball mill is an open system, hence sterility is a question D. Fibrous materials cannot be milled by ball mill. 10. What particle size can be obtained through ball mill? A. 20 to 80 mesh B. 4 to 325 mesh C. 20 to 200 mesh D. 1 to 30 mm. ANSWERS:-1. Both B and C 2. Optimum speed 3. Longitudinal axis 4. Both 5. A – 3 B – 4 C – 2 D – 1 6 ...
More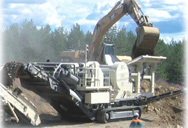
Ball mill - Wikipedia
A ball mill, a type of grinder, is a cylindrical device used in grinding (or mixing) materials like ores, chemicals, ceramic raw materials and paints. Ball mills rotate around a horizontal axis, partially filled with the material to be ground plus the grinding medium. Different materials are used as media, including ceramic balls, flint pebbles ...
More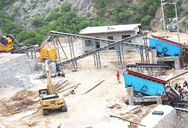
Improving product quality in pharmaceutical ball milling
2021.8.2 Ball milling is a technique that is utilised by the pharmaceutical industry for granular size reduction of drugs or excipients. There are many reasons to mill particulate materials. Very often, the milled product is required to have a specific surface area, or it might be a process requirement that the fragments are consistent in shape ...
More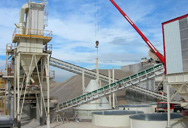
Haas Learning Resources - Haas Automation Inc.
Haas Learning Resources. We’ve created a single location to access all of the resources Haas has available to help you learn to operate and program a Haas machine, and take full advantage of the power and capability of the Haas control. You’ll find operator-certification courses, manuals, training documents, videos, and more – all right here.
More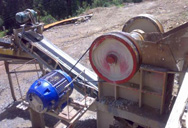
Ball mill PPT - SlideShare
2015.4.23 7. The ball mill is used for grinding materials such as coal,pigments,and fedspar for pottery. Grinding can be carried out in either wet or dry but the former is carried out at low speeds. The advantages of wet grinding are less power consumption,increased capacity,no dust formation etc. Dis advantages are high wear on the grinding medium ...
More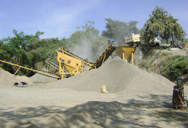
Ball Mill: Operating principles, components, Uses, Advantages and
2022.11.30 Advantages of Ball Mills. 1. It produces very fine powder (particle size less than or equal to 10 microns). 2. It is suitable for milling toxic materials since it can be used in a completely enclosed form. 3. Has a wide application. 4. It can be used for continuous operation.
More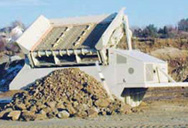
Ball Mill - an overview ScienceDirect Topics
The history and necessity of mechanical alloying. M. Sherif El-Eskandarany, in Mechanical Alloying (Second Edition), 2015. 2.5.1.5 Planetary ball mills. The Planetary ball mills are the most popular mills used in MM, MA, and MD scientific researches for synthesizing almost all of the materials presented in Figure 1.1. In this type of mill, the milling media
More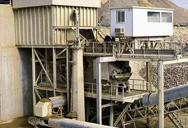
Process Training Ball Mill - INFINITY FOR CEMENT EQUIPMENT
The better mills on the market have an efficiency of about 8-9 % which means that only 8-9 % of the energy results in grinding and the majority is converted mainly into heat. The ball mill has the worst efficiency of all types of mills on the market. Just 4 % of the energy is used for comminution. Nevertheless when grinding is required the ball ...
More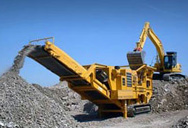
Ball Mill Design/Power Calculation - 911 Metallurgist
2015.6.19 The basic parameters used in ball mill design (power calculations), rod mill or any tumbling mill sizing are; material to be ground, characteristics, Bond Work Index, bulk density, specific density, desired mill tonnage capacity DTPH, operating % solids or pulp density, feed size as F80 and maximum ‘chunk size’, product size as P80 and
More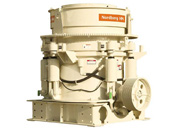
Training seminars and courses FLSmidth Institute
You can participate in our training courses online, on-site, or at one of our facilities throughout the world. Our highly skilled specialists offer unique, hands-on training designed to improve your knowledge and plant productivity, from general equipment maintenance and operations through process controls and system optimisation.
More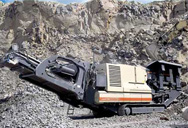
Ventilation Prediction for an Industrial Cement Raw Ball Mill by
2021.6.10 1. Introduction. In the cement industry, grinding is one of the most consuming energy stages in the production units. Around 65% of the total used electrical energy in a cement plant has to be utilized to grind raw materials, coal, and clinker [1,2].Through the process, many variables can affect the efficiency and productivity of
More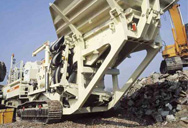
AMIT 135: Lesson 8 Rod Mills – Mining Mill Operator
Reduction ratio = 2 – 20 depending on material. Typically R = 8. Rod Mill Charge: Typically 45% of internal volume; 35% – 65% range. Bed porosity typically 40%. Height of bed measured in the same way as ball mills.
More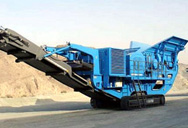
BALL MILL MAINTENANCE - The Cement Institute
2023.11.20 Module 1: Welcome and Plant Safety. Module 2: Grinding Systems and Mill Components. Module 3: Ball Mill Inspection and Lubrication. Module 4: Ball Mill Drives. Module 5: Ball Mill Separators, Types, and its Maintenance. Module 6: Fan Design and Applications. Module 7: Introduction to Conveyors. Module 8: Ball Mill Dust Collector.
More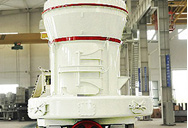
Ball Mill And Air Classifier Production System - EPIC Powder
Product Feature. 01. With Al2O3 or silex or steel lining.Mainly designed with overflow type or grate discharge wall. 02. With air through the mill or with air-swept principle to get cooler and take out ground material. 03. Inlet chute for ball mill includes accessory for feeding grinding aid directly into the mill drum. 04.
More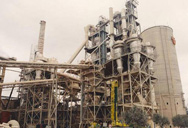
Ball Mills Training Manual: Dirección Técnica PDF Mill ... - Scribd
In the majority of the mills, the material that is rejected by the dynamic separator is introduced into the first mill chamber along with the fresh feed. ... 28/102 BALL MILLS DIRECCIÓN TÉCNICA TRAINING MANUAL. Because ball mills are exposed to many different kinds and conditions of operations, ...
More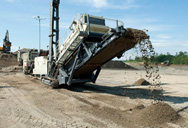
ATTRITORS AND BALL MILLS HOW THEY WORK Robert E.
Ball mills work well on hard, brittle materials. They are not as suitable for grinding elastic, ductile or fibrous materials, or for fine grinding in general. Ball mills can blend and grind at the same time, yielding a fine, intimate mixture. Conventional ball mills are usually limited to a particle size of 1µ after one hour of grinding
More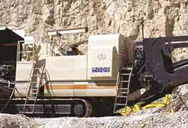
Impact energy of particles in ball mills based on DEM simulations
2022.1.1 Introduction. Ball mill is one of the most commonly used mills for the crushing and grinding of mineral ore. It is generally used to grind material down to the particle size of 20 to 75 μm and can vary in size from a small batch mill up to a mill with outputs of hundreds of tonnes per hour.
More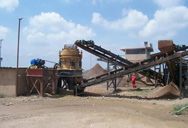
A new methodology to obtain a corrected Bond ball mill
2022.10.1 The standard Bond ball mill test requires a material of appropriate granulometric composition, 100% −3.35 mm created by a stage-crushing process, ... examination to confirm the validity and accuracy of the presented methodology for data not included in the empirical “training data” used to derive the model.
More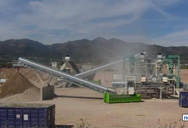
Mechanism characteristic analysis and soft measuring
2018.11.1 Mill load can be represented by using the load parameters, such as material-to-ball volume ratio (MBVR), pulp density (PD), and charge volume ratio (CVR), inside the ball mill. Studies have shown that maintaining the optimized recycle load for the grinding process improves 2–10% processing capacity, reduces 5% to −10% energy
More