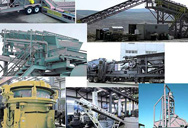
(PDF) MPS mills for coal grinding - ResearchGate
2014.1.1 PDF Two mill systems are employed for most coal grinding applications in the cement industry. These are, on the one hand, vertical roller mills (VRM)... Find,
More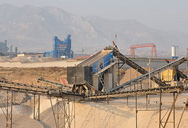
An investigation of performance characteristics and
2020.8.12 PDF This study shows the performance of a currently running vertical roller coal mill (VRM) in an existing coal-fired power plant. In a power plant,... Find, read and cite all the...
More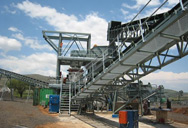
Grinding process within vertical roller mills: experiment
2009.1.1 Four grinding circuits are used with different materials: vertical mills (Loesche) for coal and cement feed; vertical roller mills for cement clinkers; and ball
More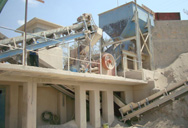
COAL GRINDING IMPS: more than meets the eye - Gebr. Pfeiffer
Vertical roller mills are not only used for grinding cement raw materials but also find an application in grinding a wide variety of coal types in cement and power plants. Gebr
More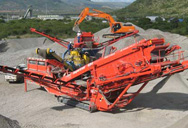
An investigation of performance characteristics and
2020.8.12 As the significant ancillary equipment of coal-fired power plants, coal mills are the key to ensuring the steady operation of boilers. In this study, a fault diagnosis model was proposed on the ...
More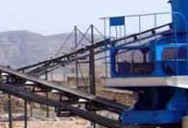
PROCESS CONTROL FOR CEMENT GRINDING IN VERTICAL ROLLER
38]. Various grinding laws, energy relationships, control factors and controller design for cement grinding are discussed in [37]. Figure-1. Vertical roller mill for cement grinding [13]. VRM shown in Figure-1 uses hydraulically hard-pressed conical shape 2-4 rollers against the horizontal revolving grinding table. To enhance comminution, the
More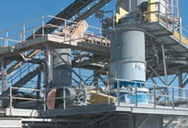
Roller Mill - Springer
R Roller Mill Xiao Xiao1, Huang Lilong2 and Xu Kuangdi3 1Changsha Research Institute of Mining and Metallurgy, Changsha, China 2Changsha Research Institute of Mining and Metallurgy, Changsha, China 3Chinese Academy of Engineering, Beijing, China Roller mill is a type of grinding equipment for crushing materials by pressure between two or
More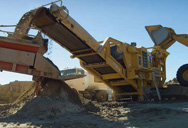
Loesche Technology - Always a Step Ahead: Loesche Mills
2014.11.5 LOESCHE-MILLS FOR CEMENT RAW MATERIAL. 3. 2 Cement raw material has been almost exclusively ground in roller mills (vertical air-swept grinding mills) since the sec- ond half of the 20th century. Loesche was and is the pio- neer of this technology. Hundreds of Loesche mills have been used in the cement industry across
More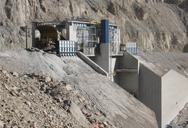
Energy-Efficient Technologies in Cement Grinding IntechOpen
2015.10.23 In this chapter an introduction of widely applied energy-efficient grinding technologies in cement grinding and description of the operating principles of the related equipments and comparisons over each other in terms of grinding efficiency, specific energy consumption, production capacity and cement quality are given. A case study
More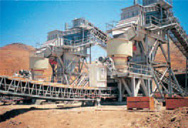
A Comprehensive Guide to Ball Mill Manual
A ball mill is a crucial piece of machinery used in grinding and mixing materials in various industries. It works by rotating a cylinder with steel or ceramic balls, causing the balls to fall back into the cylinder and onto the material to be ground. Ball mills are used extensively in the mining, construction, chemical, and pharmaceutical ...
More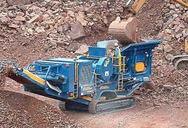
Loesche Grinding Technology for the Power Industry - Ammermann
Lift of Grinding Roller Loesche mills for solid fuels New or refurbished plant, Loesche have the mill to meet your needs Loesche vertical roller mills for solid fuels are offered with 2, 3 or 4 rollers with a capacity range of 8 to 240 t/h (16,000 to 640,000 lb/h) giving us the flexibility to match the process requirements for your plant.
More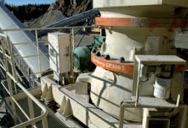
Research of iron ore grinding in a vertical-roller-mill
2015.3.15 The application of vertical-roller-mills (VRM’s) for ore grinding is part of the second strategy. The grinding parts of a Loesche mill ( Fig. 1) are a rotating table (1) with a horizontal grinding track and rollers (2), which are pressed onto the table by lever arms and a hydro pneumatic spring system.
More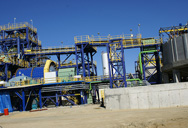
Coal Grinding - Cement Plant Optimization
Coal Grinding. To achieve good combustion and satisfactory flame formation, coal needs to be dried and ground to a proper degree of dryness and fineness. Drying of moisture in coal is achieved normally by ducting part of the kiln exhaust gas through the mill with inlet temperatures of up to 300°C. Inert kiln exhaust gases with oxygen content ...
More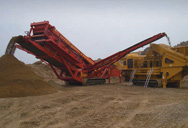
LOESCHE-MILLS
this are deployed in Klingenberg, Europe’s first coal dust-fired large-scale power plant in Berlin for coal grinding with a raw coal rate of approx. 12 t/h. 1934 Loesche mills are increasingly also used worldwide for limestone and cement raw material. 1937 400 Loesche mills have already been sold for coal, phosphate and cement raw material.
More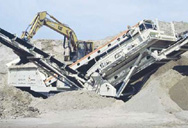
Lab-scale roller table mill for investigating the grinding behaviour
1999.11.1 For a general consideration s should be related to the roller diameter D. In coal mills this relative gap width is in the range between 0.005 and 0.025. Transferring this to the test mill, the gap should be between 0.5 and 2.5 mm. Fig. 8 shows that the measured gap widths lie in this range.
More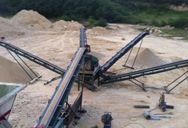
Grinding process within vertical roller mills: experiment and ...
2009.1.1 This paper describes the simulation of the grinding process in vertical roller mills. It is based on actual experimental data obtained on a production line at the plant and from lab experiments. Sampling and experiments were also carried out in a power plant that has four ball-mill circuits used for coal grinding so that different equipment ...
More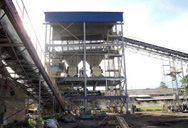
Roller Mill Agricultural Lime Procesing Plant Crusher Mills, Cone ...
Lime grinding plant with Vertical roller mills KTM 1200 Gulin machine in iron ore processing plant, coal grinding mills and conical pulverizer machine for coal lime stone MTW Trapezium Series Mill; Vertical Roller
More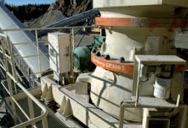
(PDF) LEARNING FROM OTHER INDUSTRIES; WHY THE VRM
2019.4.16 Vertical roller mills (VRM) have been used extensively for comminuting both cement raw materials and minerals like limestone, clinker, phosphate, manganese, magnesite, feldspar and titanium.
More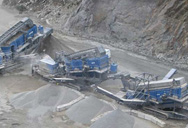
132 Loesche Mills For Solid Fuels Coal Mill E 2016 - Scribd
2019.7.18 Loesche mill Type LM 28.2 D, Detroit Thermal Energy,Vicksburg / Mississippi, USA, 2005. Loesche coal-grinding mills are adapted to individual customer Bituminous coal grinding. requirements. A change in feed material can be achieved with- Bituminous coals are the most frequently used fuels. They are.
More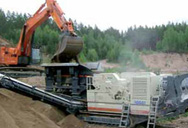
Cocoa Pulverising Machine Design, Calculations and Analysis
conical rollers with shallow bowl; deep bowl, etc. where load is applied on the rollers and the bowl rotates while pulverizing. These types of mill are designed normally up to 60 tons per hour for a specific coal; however there are vertical mills with 90 tons per hour output. A vertical spindle mill is also designed for
More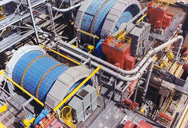
Powder mill, Powder grinding mill - All industrial manufacturers
5X Pendulum Roller Grinding Mill Thin-oil lubricating system, ... Coal powder the air swept mill is suitable for coal grinding. When the rotary kiln operates with coal powder as ... Compare this product Remove from ... -30% over traditional conical mills •Redesigned conical screen chamber •Low noise, up to -~75 dbs •CIP (clean in place ...
More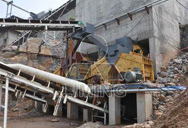
What does a Raw Mill do in Cement Plant? - ball mills supplier
The grinding plate is powered by an electric motor that rotates the plate at a speed of around 20-30 RPM. Grinding Rollers. The grinding rollers are the components that press down on the grinding plate and crush the raw materials. They are usually made of steel and are between 0.5-2 meters in diameter. Hydraulic System
More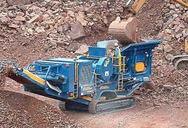
VRM Operation and Optimization PDF Mill (Grinding) - Scribd
Operation and. Optimization vertical mill used for pre grinding of clinker (lumps to coarse powder) finish grinding (lumps to powder ) of - coal/petcoke for kiln - raw material for kiln - cement, OPC or mixed - slag, pure or mixed vertical mills comprise 2-4 conical rollers which are hydraulically pressed onto a horizontal rotating grinding table the roller axis is
More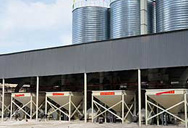
An energy based comparison of vertical roller mills and tumbling mills
2015.3.10 The Institute of Mineral Processing at the Montanuniversitaet Leoben in cooperation with the company CEMTEC has developed a pilot scale, 200 mm table diameter, vertical roller mill for energy controlled laboratory tests.The mill provides the technical options to vary process parameters like air-flow, mass flow, grinding force and
More