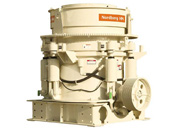
Crushing and grinding process for treating nickel-copper sulfide ore
The invention relates to the technical field of metal mineral processing, in particular to a novel ore crushing and grinding process, and particularly relates to a crushing and
More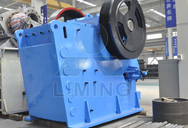
Processing of oxidized nickel ores using sintering, roasting and ...
2022.5.15 The article is devoted to the results of research into the process of sintering, roasting and leaching of oxidized nickel ores, with selection of optimal
More
Crushing and Grinding Wet Sticky Ore - 911 Metallurgist
2016.5.9 Crushing and Grinding Wet Sticky Ore In the handling of wet, sticky ores such as encountered in tropical areas having distinct dry
More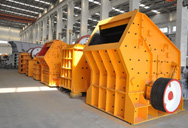
Mineral Liberation - an overview ScienceDirect Topics
This is done by crushing and grinding the ores to liberate the nickel- and cobalt-bearing minerals from the other minerals. The ground ore is processed through two stages of flotation. The first stage of froth flotation separates the nickel-, cobalt-, and copper-bearing minerals from the gangue rock and pyrrhotite.
More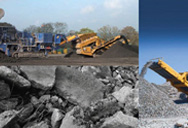
Crushing and grinding process for treating nickel-copper sulfide
The invention discloses a crushing and grinding process for treating nickel-copper sulfide ore, and belongs to the technical field of metal mineral processing. The grinding process comprises the following specific process steps: semi-autogenous grinding → wet screening → obstinate stone crushing → cyclone classification → ball milling classification.
More
(PDF) Potential Processing Routes for Recovery of
2017.11.6 At the same time, hydrometallurgical techniques are often considered as alternative approach for treatment of low-grade sulfide ores and substandard concentrates containing copper, nickel, and PGM ...
More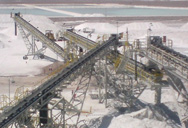
(PDF) Variability Study of Bond Work Index and Grindability Index
2021.6.17 Abstract and Figures. It is a well-known fact that the value of the Bond work index (wi) for a given ore varies along with the grinding size. In this study, a variability bysis is carried out with ...
More
METALLURGICAL TESTING METHODS (RENISON, TASMANIA
2 SAMPLE PREPARATION, CRUSHING AND GRINDING 2.1 Introduction This section of the laboratory manual discusses aspects of sample preparation as well as operating details of individual crushing, grinding and classification equipment. The individual steps outlined are recommended for guidance purposes. A suggested time frame, where
More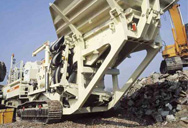
Mineral processing - Wikipedia
Crushing, a form of comminution, one of the unit operations of mineral processing. Mineral processing is the process of separating commercially valuable minerals from their ores in the field of extractive metallurgy. [1] Depending on the processes used in each instance, it is often referred to as ore dressing or ore milling .
More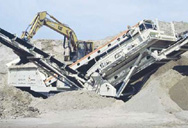
OVERVIEW OF MINERAL PROCESSING METHODS - ResearchGate
7 2.5 Grinding is the stage of size reduction (wet or dry) where the liberation size for individual minerals can be reached. Size reduction by crushing has a size limitation for the final products.
More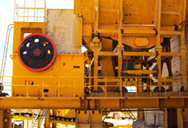
The Extractive Metallurgy Industry SpringerLink
2021.8.10 2.4.2.1 Crushing/Grinding. Ores often occur in nature as big lumps that are not directly suitable for most extraction ... simple cyanide and weak cyanide complexes of zinc, cadmium, silver, copper and nickel. The third form is total cyanide, which includes all forms of cyanide (free and complex) including iron, gold, cobalt and ...
More
Copper processing - Ores, Refining, Smelting Britannica
In mixed ores, nickel, zinc, or lead can accompany the copper; when such ore is mined, these other metals also are ... For sulfide ores, on the other hand, selective flotation normally follows the crushing and grinding stage and requires an optimal degree of liberation. Schematic diagram of a flotation separation cell. In the flotation ...
More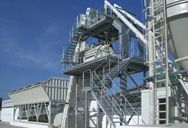
Copper Ore Crushing, Grinding Flotation - 911 Metallurgist
2017.5.21 Grinding and Flotation. Fine ore at minus 19mm (¾”) sizing is fed at a controlled rate into the open-circuit 2600mm x 3960mm (8’-6 x 13’-0) Hardinge rod mill at an average feed rate of 2,106 STPD or 87.75 STRH. Rod mill discharge at a nominal size of minus 16 mesh and a pulp density of 75 percent solids combines with ball mill discharge ...
More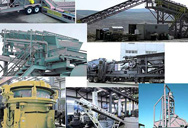
Crushing Energy Efficiency - North American Mining Magazine
2021.6.10 In particular, the decarbonized economy is going to require copper for electricity transmission; lithium, nickel, ... $5 million for the team that demonstrates the best energy breakthrough in crushing and grinding. ... energy efficiency gains, particularly when grinding higher competency ores. Pictured: Weir’s Enduron HPGR ...
More
(PDF) Comminution in mineral processing
2018.11.19 Crushing and grinding are commonly known as size reduction process (comminution) in . mineral processing which helps to reduce the huge energy consumption and lower the costs to .
More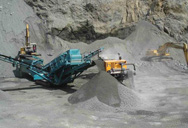
Evaluating the performance of an industrial-scale high pressure ...
2023.1.1 HPGR utilising a particle-bed crushing mechanism to generate finer products has gradually acquired a reputation in the metal mining industry (Van Drunick and Smit, 2006), for its selective fracture ability (Ma et al., 2021) and creating microcracks within grains to reduce specific energy consumption in the downstream grinding process
More
Nickel and Cobalt Production - ScienceDirect
2014.1.1 This is done by crushing and grinding the ores to liberate the nickel- and cobalt-bearing minerals from the other minerals. The ground ore is processed through two stages of flotation. The first stage of froth flotation separates the nickel-, cobalt-, and copper-bearing minerals from the gangue rock and pyrrhotite.
More
Nickel (Ni) Ore Properties, Formation, Minerals, Deposits
2023.4.23 Nickel ore refers to the naturally occurring rocks or minerals that contain significant amounts of nickel. Nickel is a chemical element with the symbol Ni and atomic number 28. It is a silvery-white metal with a relatively high melting point and excellent corrosion resistance. Nickel is commonly found in the Earth's crust, but it is typically
More
Preconcentration strategies in the processing of nickel laterite ores
2015.4.2 Despite the growth in nickel laterite processing, upgrading these ores remains a challenge. This is mainly because of their complex and variable mineralogy and the lack of definite nickel-bearing ...
More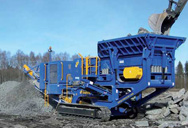
Processing of oxidized nickel ores using sintering, roasting and ...
2022.5.15 Compared to the copper ores, nickel ores are characterized by high absorption of sulfuric acid at the level of 300–700 kg per ton of ore (Kolmachikhina et al., ... Ore samples were averaged, followed by crushing and grinding. During sintering, binders were added to the crushed ore. In addition to the base ore, ...
More
2 Types of Nickel Ore: Processing Methods and Equipment
2023.4.25 1.1 Copper-nickel sulfide ore crushing stage. Adopt a two-stage closed-circuit crushing process. ① Use a jaw crusher for primary crushing. ② Use a cone crusher for fine crushing. ③ Use a vibrating feeder to screen out the products whose size meets the grinding requirements, while the oversized ones are returned to the cone
More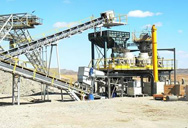
Crushed ore agglomeration and its control for heap leach
2013.2.1 Most ores not containing excessive clay will percolate well when crushed as fine as 10 mm. It is possible to heap leach gold locked in some sulfide ores by adopting a bio-oxidation pretreatment followed by heap leaching. When gold is locked in other minerals exposure and leaching is possible by fine crushing using HPGR (Alta, 2011). Ideal ...
More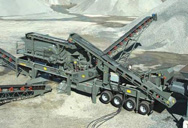
Hydrometallurgy SpringerLink
2021.6.23 Hydrometallurgy refers to the extraction of metals and production of inorganic substances from minerals through aqueous solutions. Although the entire amount of iron, lead, tin, and antimony and major production of copper and nickel come from the pyrometallurgical route, hydrometallurgy plays an important role in the extraction of
More